Moisture mitigation in your concrete substrate is the key to building epoxy floor systems that perform and last. Not taking the proper steps to protect your facility from moisture vapor transmission can cause expensive problems for your epoxy floors like bubbles, delamination, and even shortening the lifespan of your flooring.
For unmatched industry knowledge and expertise, trust Epoxy Coating Specialists for impactful moisture mitigation techniques and services. We have the tools necessary to assess the job, take proper precautions, and prevent moisture-related damage for the life of your epoxy system. Keep reading to learn more about our moisture mitigation process.
What causes bubbles in epoxy floors?
Bubbles are caused by moisture vapor transmission beneath the epoxy coating. When proper moisture mitigation precautions aren’t taken during the pre-construction process, it can lead to residual moisture in the substrate of your facility. Installing an epoxy coating on top of this substrate can trap the moisture, causing bubbles and further damage over time.
While bubbles may not sound too serious, correcting the issue often takes thousands of dollars worth of work. Taking the cheap route in your pre-construction plan could be a costly choice in the long run.
No matter your facility’s circumstances, Epoxy Coating Specialists (ECS) possesses the right skills and tools to help you mitigate moisture and build an epoxy floor system that lasts. When we take on a project, we look for two main sources of moisture:
New construction
The most common source of moisture is recently poured concrete. A newly built or renovated facility where the substrate or slab has recently been laid is more likely to have excess moisture, and therefore experience bubbling due to moisture vapor transmission.
Excess moisture often comes from the concrete internally, as water is mixed with concrete in the pouring process. After the concrete is cured and dried, it needs additional time for the internal moisture to evaporate before it’s coated. If a coating is applied while the concrete retains this excess moisture, you might end up with bubbles in your epoxy floor.
A general rule of thumb we follow is: it takes approximately 40 days per inch of concrete to get moisture levels low enough to provide an epoxy coating without having to apply a moisture mitigation system.
Additionally, older facilities did not always have the same moisture-preventing requirements during construction. Nowadays, it’s standard practice to use a high-performance, below-slab vapor barrier. For example, Stego Wrap, a leader in the industry, is used to protect the building envelope from below-slab moisture vapor, soil biases, and other contaminants.
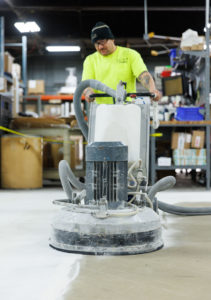
Wet environment
Environmental factors may also greatly influence the moisture levels in and around your project. Moisture from the ground underneath your building may pose a risk to your flooring if you live in an especially humid climate, or experience high precipitation levels.
ECS has experience with all kinds of projects, including preventing bubbles in epoxy floors for a wide variety of customers. No matter the location of your facility, our specialists can expertly assess the project and determine which moisture mitigation strategies are the best fit for you.
How to prevent moisture problems bubbles in epoxy floors
Preventing bubbles in epoxy floors, or any other moisture-related damage, starts from the first consultation. ECS builds custom flooring solutions, and that includes moisture mitigation strategies that set your project up for lasting success. Here are the steps we take:
Step 1: On-site consultation
To kick-off your project, we send a representative to your location for an on-site consultation. Seeing the facility in person allows us to put together a detailed scope of the project, and propose a unique flooring solution that addresses your needs and performs for your unique operations.
An in-person consultation also allows us to identify potential problems, before they become costly, long-term problems. A strong, well-designed concrete slab is the best base for any flooring system, but has to be properly qualified before any coating system is applied.
Step 2: Moisture testing
Part of our initial on-site consultation is a moisture evaluation. This evaluation allows us to indicate which moisture test and flooring system would be the best fit for your facility, and also alert us to any pre-construction steps we might need to take before pouring your epoxy. We want to provide you with moisture mitigation solutions before proposing a flooring plan.
It’s important to note that moisture tests are subjective to the time the measurements were taken. Tests cannot account for future moisture levels, they are simply a snapshot in time and could ultimately be affected by:
- Weather conditions
- Season
- Climate
- Proximity to other projects
- Building history
- Age
- Poor plumbing
- Poor drainage below the slab
When choosing which type of moisture test to perform, we rely on manufacturer recommendations based on the type of your concrete. Here are the different types of moisture tests, in order from least to most comprehensive.
Tramex moisture meter (ASTM73191)
The Tramex moisture meter is a handheld machine that measures current moisture level in and around your concrete foundation. The device is held up against the concrete and gives an instant reading.
This test is a basic, standard option and may be performed as a preliminary test to determine if further testing is required. The Tramex gives us an instant reading and, based on its results, your consultant will make further recommendations.
Calcium chloride test (TM710)
A calcium chloride test requires some additional materials. It begins with mechanically preparing an area of concrete. We then “glue” down a dome and fill it with moisture-absorbing calcium chloride bb’s. How quickly the bb’s fill up with moisture indicates the amount of moisture leaving the concrete in the form of vapors, which could negatively impact the flooring you lay on top if there is too much.
Relative humidity test (ASTM2659)
A relative humidity test is a deeper dive into the moisture within your concrete. We drill a whole down into the slab and insert a probe with a reading device. The probe sits for a full 24 hours and takes a measurement of moisture levels and temperature. Both of these factors are important in determining how your foundation will affect the epoxy coating process.
Step 3: Epoxy floor system proposal
Within 48 hours after the consultation is complete, you will receive a custom, detailed proposal from your project manager. It will include:
- Project area (square-footage)
- Two flooring system options for you to choose from: best and value
- Project schedule as determined by you
- Project phases (projects can typically be completed in one continuous phase, unless otherwise outlined by you due to schedule or other limitations)
- Price estimate
- Any additional notes from your consultation
- Warranty information
- Our ECS terms and conditions for your reference
After receiving the proposal, you can still consult with your Epoxy Coating Specialists representative to make your custom project fit your time and budget. One way or another, we can find a solution to get you the flooring system option that works best for you while taking the proper steps to prevent bubbles and other damage from moisture.
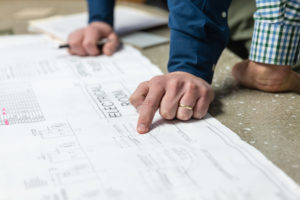
Effective moisture mitigation strategies
Once your site’s level of moisture has been addressed and measured, we can take steps towards mitigating and preventing bubbles in your epoxy floor. Just like your project proposal, moisture mitigation strategies are custom-built based on the needs of your facility.
Pre-coating your epoxy floors
If tests indicate that your foundation has high moisture levels, your project manager will recommend a moisture vapor reducer as a pre-prime coating. This pretreatment will act as a barrier between your concrete and the epoxy for added protection.
Your proposal will also include a specific number of coats of moisture vapor reducer based on your facility’s test results and scope of the project. The number of coats is often based on the readings of moisture tests described above.
Urethane cement
Urethane cement overlay from ECS is a durable, customizable flooring option. The cement overlay mixture is actually a blend of cement, other aggregates, and polymer resin, which increases performance and adaptability. The mixture is laid over your existing concrete up to a quarter-inch thickness, and is oftentimes your best insurance against any moisture related problem.
Urethane cement is especially designed to withstand moisture, making it an ideal solution for facilities with excess moisture in their existing foundation. Our expert team tailors your urethane cement flooring to the specifications of your building, providing you with a fail-safe in your system and dependable flooring that lasts.
Product additives for breathability
The reason moisture mitigation is so essential before epoxy coating is because epoxy is not inherently a breathable material. Epoxy is traditionally a two-part mixture of resin and hardener, which chemically bond to create a hard plastic surface that is durable and resistant. This is what makes it an ideal option for facilities, but it’s also what traps excess moisture beneath its surface, creating bubbles in epoxy floors.
ECS offers a special line of breathable epoxy coatings for facilities struggling with excess moisture. Your project manager can help you determine if this extra step is right for you.
What to do if you have bubbles in your epoxy floor
If you had epoxy coating done by another company in the past and are noticing bubbles, ECS can help. Unfortunately, this most often means fully removing your current flooring system and replacing it with the proper moisture mitigation strategies in place.
We understand that no one wants to hear they need to start over, but your epoxy coating will perform much better and last much longer without the effects of excess moisture. Let us help you out and see the difference ECS can make for your facility.
Get Your Project Started Now
In need of custom epoxy floors in Kansas City, or wanting the guidance of an expert to prevent bubbles in your epoxy floor? Contact Epoxy Coating Specialists today or use our free online Get a Quote tool!
We are the number one flooring services choice for businesses in Kansas City and across the midwest. Start your project now and experience the Epoxy Coating Specialists difference.